加气块/板材生产线设备之配料浇注及搅拌控制系统
发布时间:
2025-01-09
在上文中给大家介绍了加气块/板材生产线设备的原料预处理系统,本文就为大家介绍一下加气块生产线的配料浇注及搅拌控制系统。配料浇注及搅拌控制系统主要是由浇筑搅拌机、铝粉自动计量装置、气泡整理机组成的。下面就为大家详细介绍一下。
浇注搅拌机
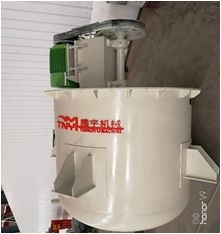
浇注搅拌机采用螺旋式搅拌机(乌尼泊尔专利技术),螺旋浆配合倒流筒会使料浆上下翻腾,使得物料混合的更加均匀,达到非常好的搅拌效果。浇注搅拌机位于模具上方,是生产线的重要装备之一,直接决定产品的成型质量。
主要特点:
搅拌器采用十字螺旋浆式搅拌器,寿命长,故障率低,搅拌速度快,搅拌均匀;
搅拌机采用四点式减震,搅拌时震动小;
采用改良式导流筒,内壁设置4块阻流板,干料不会堵塞,搅拌更加均匀,改善下料效果,缩短浇注周期保证5分钟之内完成模箱浇注
放料采用升降式浇注,保证浇注环境,减少浇注时料浆对涂模油的冲击和大气泡的产生。
电机采用高效节能电机,可实现变频调速,平均节能5%左右。
主要技术参数:
容量:5.2m3 功率:55KW
铝粉自动计量装置

GY-300I型铝粉膏自动添加设备采用干粉一模一计量方式,从铝粉膏给料、计量、加水、搅拌、铝粉液放料全部自动运行。该设备具有独特的卸料机构、高精度称重传感器、智能化控制软件,可以有效的解决铝粉膏用量少,要求精度高的问题。 该装置作为配料系统中的一个独立单元,既可并联入原系统自动运行,也可以单独运行。
设备特点:
(1)精度高:精度控制在±5克以内。适用于各种粘度的铝粉膏。采用减重计量,不存在铝粉膏粘秤问题。
(2)容量大:一次填装基本可以满足一个班的铝粉膏用量。标准配置铝粉膏储罐容积约500升。
(3)性能稳定,维护方便:运行成本低PLC程序控制,结构简单,各种报警功能齐全。综合耗电量约0.6kw/h。
(4)搅拌效果好:搅拌罐锥形底设计,自动加水,边搅拌边下铝粉,搅拌均匀,放料迅速。
(5)采用PLC控制,人机交互界面,完成校称、参数设定等工作。
气泡整理机
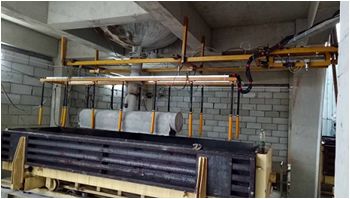
浇注过程中会有许多空气被带入料浆中,在坯体形成过程中这些空气因无法析出会形成各种不规则气孔结构,最终导致制品强度不均匀并影响制品外观质量。 原理就是采用气、液或电动执行机构推动一组安装在平面连杆支架上的插入式振动棒,按照传感器和控制开关的指令,适时插人料浆振动和提起停止振动。根据不同的工艺布局可有不同形式的气泡整理机。对于位于地面上的浇注工位,可以直接在合适的位置设置固定支架安装气泡整理机。也可直接把气泡整理机和浇注机整合在一起。
主要特点:气泡整理机配备二十个高频振动器。
聚焦热点